模具是“万业之母”,主要应用在电子、汽车、电机、电器、仪表、家电和通讯领域。我国是全球主要的注塑模具和冲压模具生产国之一,主要应用在汽车、家电、消费电子、仪器仪表、航空航天和医疗器械等产品的加工成型。根据中国模具工业协会,我国模具产业冲压模约占37%,塑料模约占43%,铸造模(包含压铸模)约为10%,锻模、轮胎模、玻璃模等其他类模具占10%,与工业发达国家的模具产业结构基本一致。
增材制造-3D打印技术其中一个显著优势是在无需模具的情况下直接制造出零部件,随着3D打印材料的发展,增材制造质量控制水平的提升,3D打印技术正在从少量原型产品的制造,向最终零部件的批量制造方向发展。
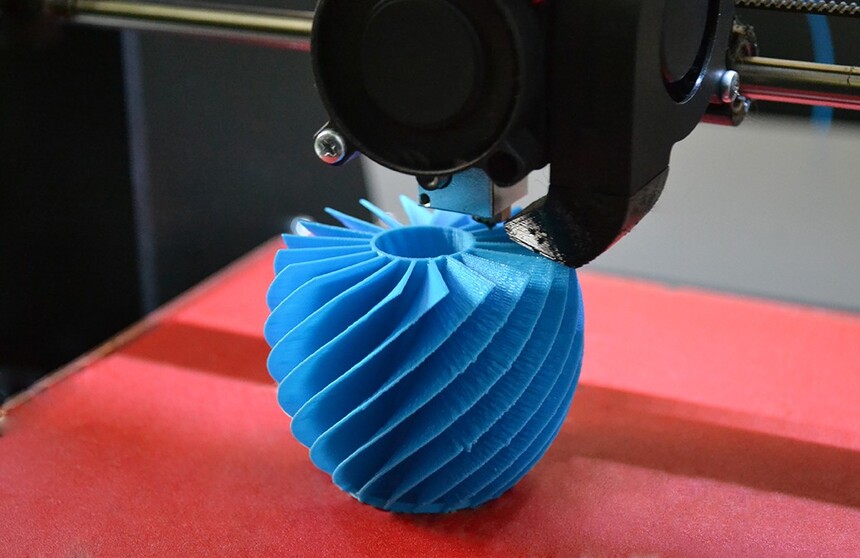
1、3D打印满足设计的无限性
模具需满足一定的精密度,可靠性及结构的复杂性(有些模具要求特定的几何形状),传统的模具制造技术落后于数字化设计的进步速度,于是便出现了设计无法完全被还原的问题,比如通过CAE设计的随形冷却水道(较多弯道),传统模具在生产弧形、弯道之类的形状时具有天然缺陷,导致设计只能“削足适履“,将冷却水道设计成直线型,最终的冷却效率当然也会打折。而3D打印可以满足设计的无限可能,在不牺牲精度和质量可靠性的前提下完全还原”异形“设计。
传统的模具制造方式要经过图纸设计、工艺审查、可制造性分析、设计工艺、编程、加工等流程,需要较多的人员和工具参与,周期漫长。3D打印通过电脑建模快速打印的方式,可以快速有效地验证设计,优化方案,加快产品的开发过程,给企业带来新产品开发和产品创新的积极性。
3D打印可以高度还原设计细节,可以制造传统模具无法企及的复杂形状,可以缩短制造周期,可以降低制造成本,3D打印的这些优点加在一起,就使得个性化、定制化模具的生产成为可能,在航空航天业里,许多精密的结构复杂的零件可以通过3D打印去突破国外的技术封锁;在医疗行业,医生对个性化器械的需求以及人体对于个体化植入骨骼的需要,可以通过3D打印来实现;在生活领域,消费者对于多样化产品的需要,可以通过3D打印来创造。
2、变与不变之间的机遇
有人疑惑,3D打印技术与模具制造技术似乎是一对矛盾, 3D打印似乎要让制造流程跳过模具这一个环节…
对于国内的模具制造企业而言,如何理性的理解3D打印对模具行业带来的威胁、挑战与机会?如何决策在“变”与“不变”中取得发展机遇的最大化?这就需要从“底层”逻辑中理解3D打印发展的运行逻辑与趋势,以及对模具带来的冲击力在何方?
从制造进化角度,宏观层面看,制造会逐步进化掉中间的冗余和繁琐的组装拼接,或许3D打印的终极发展会废除现在很多压铸、锻造用模具的存在,保留下来的是一些3D打印难以实现的超大零件或者是批量非常大零件的制造,那些必须通过传统方式加工才具备经济效益的零件所需的模具将得以保留。另外一方面保留下来的是跟电子、白色家电、日用品相关的注塑模具。无疑在朝向资源利用率更加高效、更加可持续发展的方向发展,这是支撑3D打印渗透到制造的方方面面的发展逻辑。
然而,从另一方面看,3D打印又使得模具变得更加重要了,譬如说米其林这家公司如此专注,做了这么多年的轮胎,为什么收购addup这家3D打印设备企业,米其林通过自己拥有3D打印技术来探索轮胎模具的制造,这其中的逻辑主要是因为3D打印成就复杂形状的能力,金属3D打印很好的解决了刀具干涉的问题,当复杂性与可制造性不再是困扰轮胎模具制造的最大因素的时候,3D打印很好的释放了轮胎产品设计迭代的便捷性,也催生了新型的轮胎制造能力。
国内,作为国内较早在轮胎模具制造领域引进增材制造的企业,巨轮智能目前已建成非金属(高分子复合材料)增材制造-3D打印生产线,用于生产轮胎模具基础模,一方面提升加工效率,另一方面节约材料、设备、刀具成本,具有一定的生产优势。